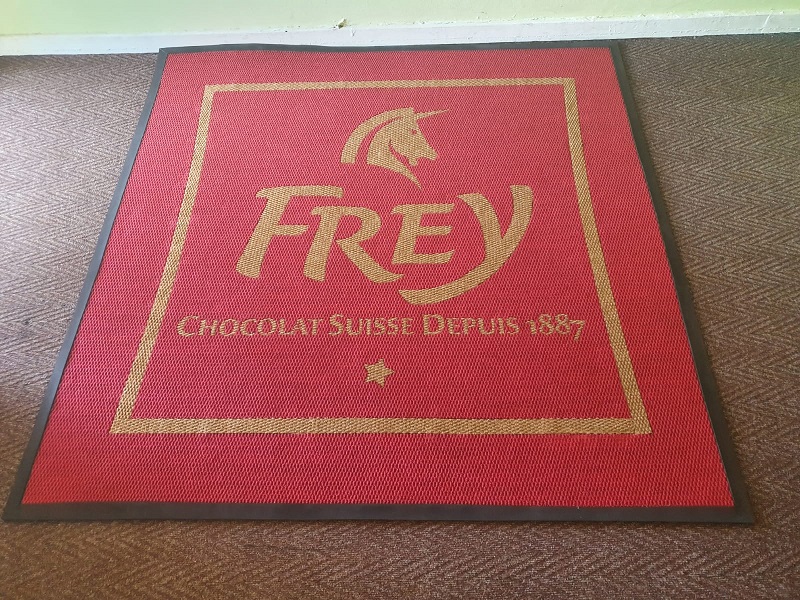
How to make a branded welcome mat
Stages of making a branded entrance mat
Step 1. Personalized entrance artwork
For one to make a personalized doormat, you have to do artwork, there are many programs that can assist one to create an artwork, the software programs can be used to assist in this regard are CorelDRAW, adobe illustrator CC, Sketch, Xara Designer Pro X, Gravit designer, and Inkscape.
The colors need to be included in the design.
Step 2. Approval of Artwork
If you can do the artwork yourself and you are content with all the logo and wording features, then you can go to the next stage.
If artwork is done by an external person or organization, then one must really examine it properly as what is designed on the artwork will be what will be produced as a mat.
Step 3 Preparation of stencil
The Artwork stencil is designed in two ways.
- Manual way
The stencil is cut into a paper into the required design that should reflect on the mat
- Computerized stencil
The stencil is downloaded on to the computer for ready use
Step 4 Production of the mat
Different mats are made using different material although most of the production process is similar. Will reveal in detail on each type of mat and how it is produced.
- Berberpoint Welcome Mat
Berberpoint mats are made from an ordinary roll of carpet material. The material is first to cut into the desired shape. If the mat is larger than the material, then joints must be made and placed together.
- Manually stenciled procedure
The stencil is placed on top of the cut mat and uses chalk to draw around the stencil shaping the words and the stencil. After the areas to be cut have been cleared marked. Take a razor knife and cut around the areas that need to be removed so that logos can be placed.
Take different colors that needs to be placed on the carpet as the logo also needs to be cut around. When all the different pieces of color material have been cut and ready.
Cut out the roll of the rubber at least 2.5mm more than the cut to make a provision for the rubber around to sit on the edges.
Take glue that is appropriate for the rubber and spread the glue on it and place it on open air for at least 30 minutes so it can dry.
Take the cut material and place it neatly on the rubber and hit the carpet onto the rubber with a rubber mallet so that they can stick together.
After that take a strip of the 2.5mm rubber and strap around the mat and hit with a rubber mallet. After the mat is finished it should be left to dry for the whole day.
- Computerized production procedure
The carpet is cut to the correct size and placed on to the Computer Numerical Control (CNC) machine bed and the carpet is laser cut according to the stencil that has been downloaded on to the machine.
The same procedure as the one for manual-based manufacturing is used that is to take different colors that needs to be placed on the carpet as the logo also needs to be cut around. When all the different pieces of color material have been cut and ready.
Cut out the roll of the rubber at least 2.5mm more than the cut to make a provision for the rubber around to sit on the edges.
Take glue that is appropriate for the rubber and spread the glue on it and place it on open air for at least 30 minutes so it can dry.
Take the cut material and place it neatly on the rubber and hit the carpet onto the rubber with a rubber mallet so that they can stick together.
After that take a strip of the 2.5mm rubber and strap around the mat and hit with a rubber mallet. After the mat is finished it should be left to dry for the whole day.
- Jet Print Mat
Jet Print Production involves a wholly computerized production system. The procedure is exactly as a photocopying machine. The carpet is cut and placed in the machine and all the mixtures of the colors are printed as per the stencil. This type of mat is one of the very few mats that can be printed with Pantone colors.
- Rubber mat/ Digi scrapper mat/ Digi-mat
This type of mat is an all rubber type of mat, it is also one of few mats that can have Pantone colors printed on them. Basically, a mold system is used whereby a mold of how the mat will look like is first designed and the rubber liquid is put into the mold and mat is printed.
This type of mat basically takes less than a minute to produce. It is produced using an injection molding machine, thus the initial capital to make this type of mat is high. It uses virgin PVC or recycled materials depending on the quality that one wants to achieve.
- Branded or Plain Spaghetti mat
Spaghetti mat manufacturing production is the same as the process of manufacturing of Berberpoint material, the difference is in the type of material and the edging type which uses flexible PVC. When all the different pieces of color material have been cut and ready.
Cut out the roll of the rubber at least 2.5mm more than the cut to make a provision for the rubber around to sit on the edges.
Take glue that is appropriate for the rubber and spread the glue on it and place it on open air for at least 30 minutes so it can dry.
Take the cut material and place it neatly on the rubber and hit the carpet onto the rubber with a rubber mallet so that they can stick together.
After that take a strip of the 2.5mm rubber and strap around the mat and hit with a rubber mallet.
After the mat is finished it should be left to dry for the whole day and should be under a flat heavy plate so that it can maintain its shape.
- Coir Mats Production
This is an easier mat to make. A roll of coir mat is cut to size. The artwork is manually designed and cut to the design of the wording and logo.
The stencil is placed on the surface of the coir mat and paints colors of different design according to the artwork is sprayed on to the coir mat until the mat design comes out clearly.